From February of 2020 to the present, Dekelbaum has been creating smaller “billets” of WTC Damascus steel by layering the WTC steel with three other types of rolled steel in accordance with the unique formula he devised and that Cabot tested. Creating the actual Damascus steel uses a solid phase diffusion bonding of the constituent metals at heats exceeding 2000f. During the process of creating the billets for these firearms, the steel is cut, restacked, and welded multiple time to achieve the desired layer counts to support the patterns created. Additionally, the forging steps taken create specific patterns in the resulting material. Though the general character of the patterns can be controlled, due to the nature of the work, no two pieces will be exactly identical. The forging work for this material is primarily performed using a hydraulic press purpose designed for forging, which exerts nearly 40 tons of pressure. For the twist pattern of the slides, Dekelbaum designed and constructed a custom twisting machine that can apply well in excess of 1500 lb/ft of torque in order to twist the massive bars required to establish the twist pattern shown in the slides. Once the final billets have been created, they are then “normalized” to create a homogenous grain structure in the steel which is conducive to the machining and further heat treatment steps required. First, however, as completed, the billets, (now essentially solid blocks of layered steel, shaped in accordance with Cabot’s requirements), had to undergo a special process to ensure that there were no tiny voids or other internal flaws in the steel. During the last week of Feb, 2020 Deker personally drove the first batch of billets he had created to Pressure Technology Inc.in Warminster PA where the requisite Hot Isostatic Pressing was performed on 2/29/2020. The following week he returned to the specialty facility Pressure Technologies Inc., picked up the 24 billets and drove them back to his shop where they were securely stored.
Meanwhile, and as the iterative process continues, the remaining “pure” 1/8” rolled WTC steel remains stored in a separate locked contained in Dekelbaum’s shop.
The normalizing and annealing process requires heating the layered steel to a temperature of 1500 degrees and then slowly cooling it, and must be done in a different specialized facility. Additionally, the hardening process for the frame billets must be completed by a third party due to the large scale of the pieces. During this process, the frame billets are heated to 1500F and cooled in a rapid quenching procedure to harden them They are then re-heated to a lower temperature to “temper” the material to arrive at Cabot’s specified hardness of 36-38HRC.
Dekelbaum personally drove the first batch of 24 layered WTC/Damascus steel billets to an heat treatment shop Bodycote in York, PA; when the heat treatment processes were completed. Dekelbaum picked the billets up and personally returned them to his shop. While at the heat treatment facility the WTC/Damascus steel was also subjected to a “hardness” test, to ensure the necessary degree of “Rockwell hardness” that is required.

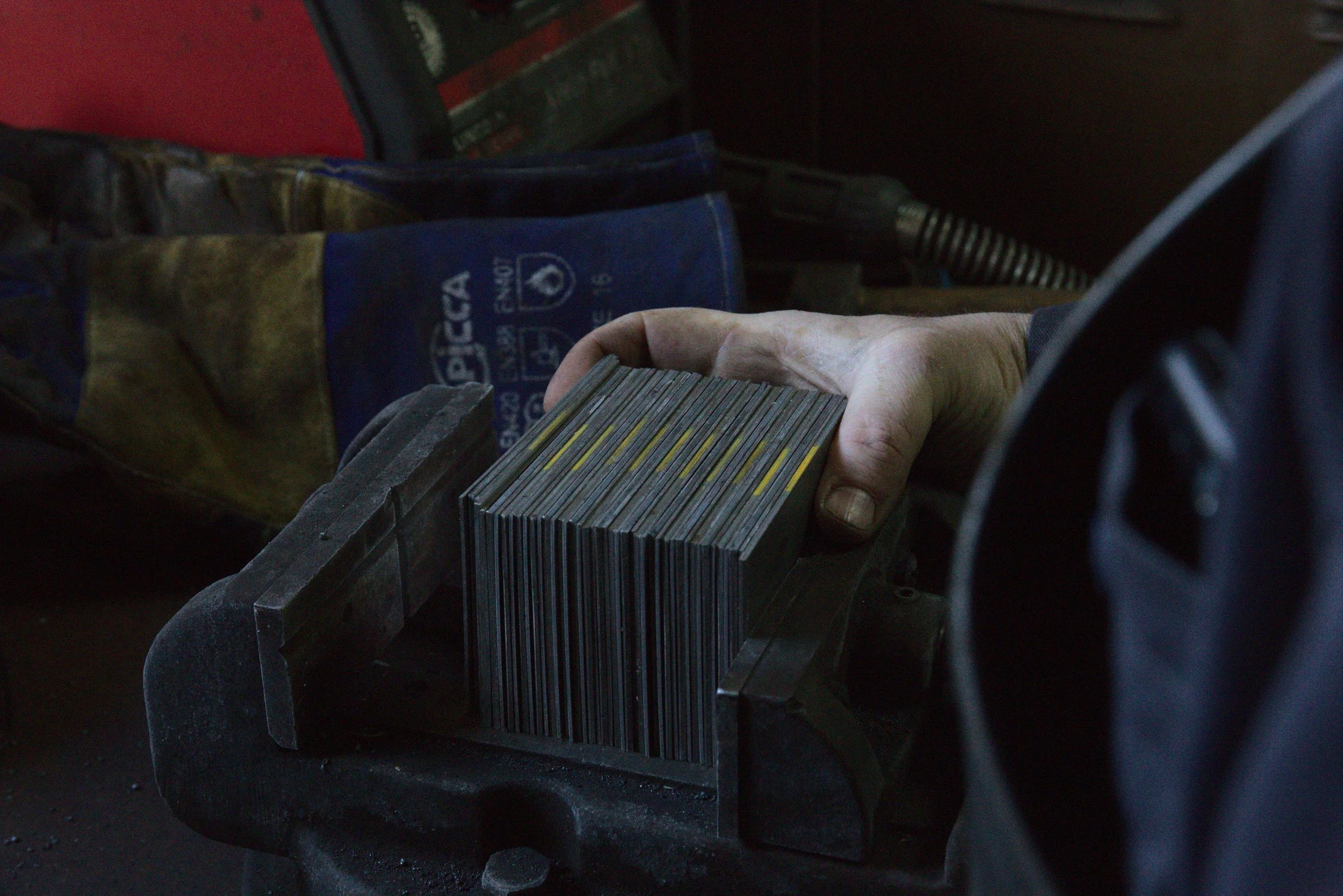
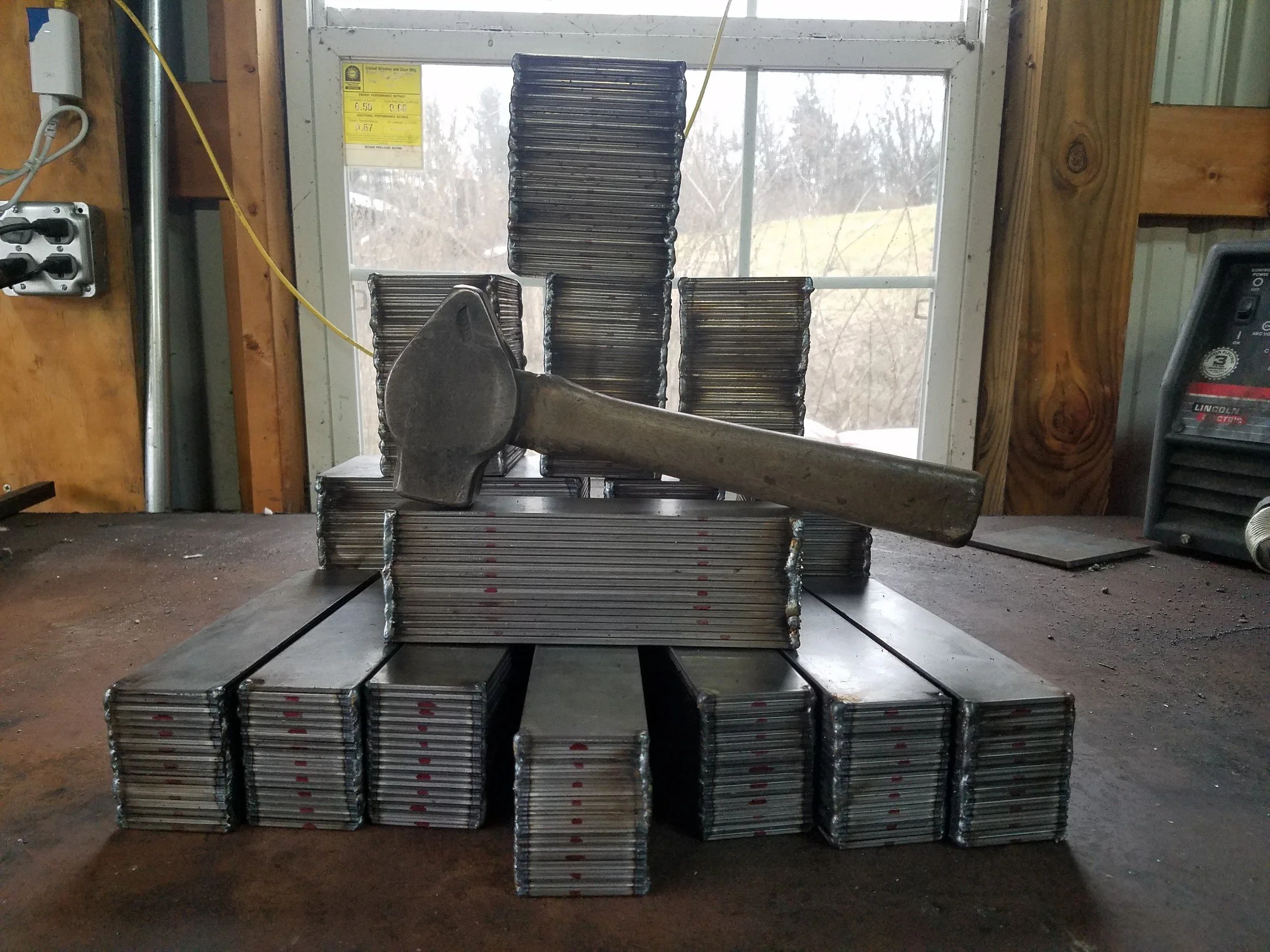
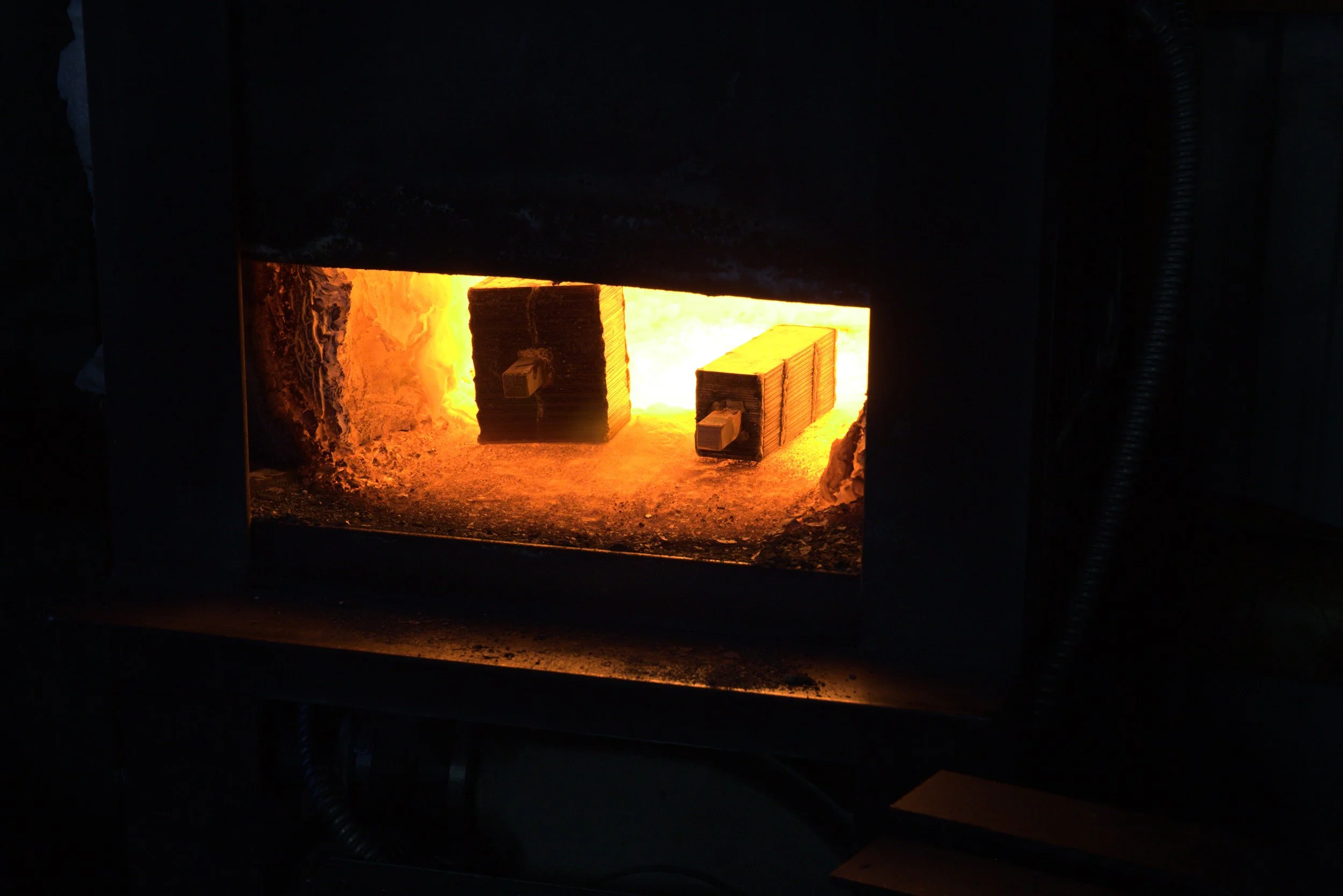

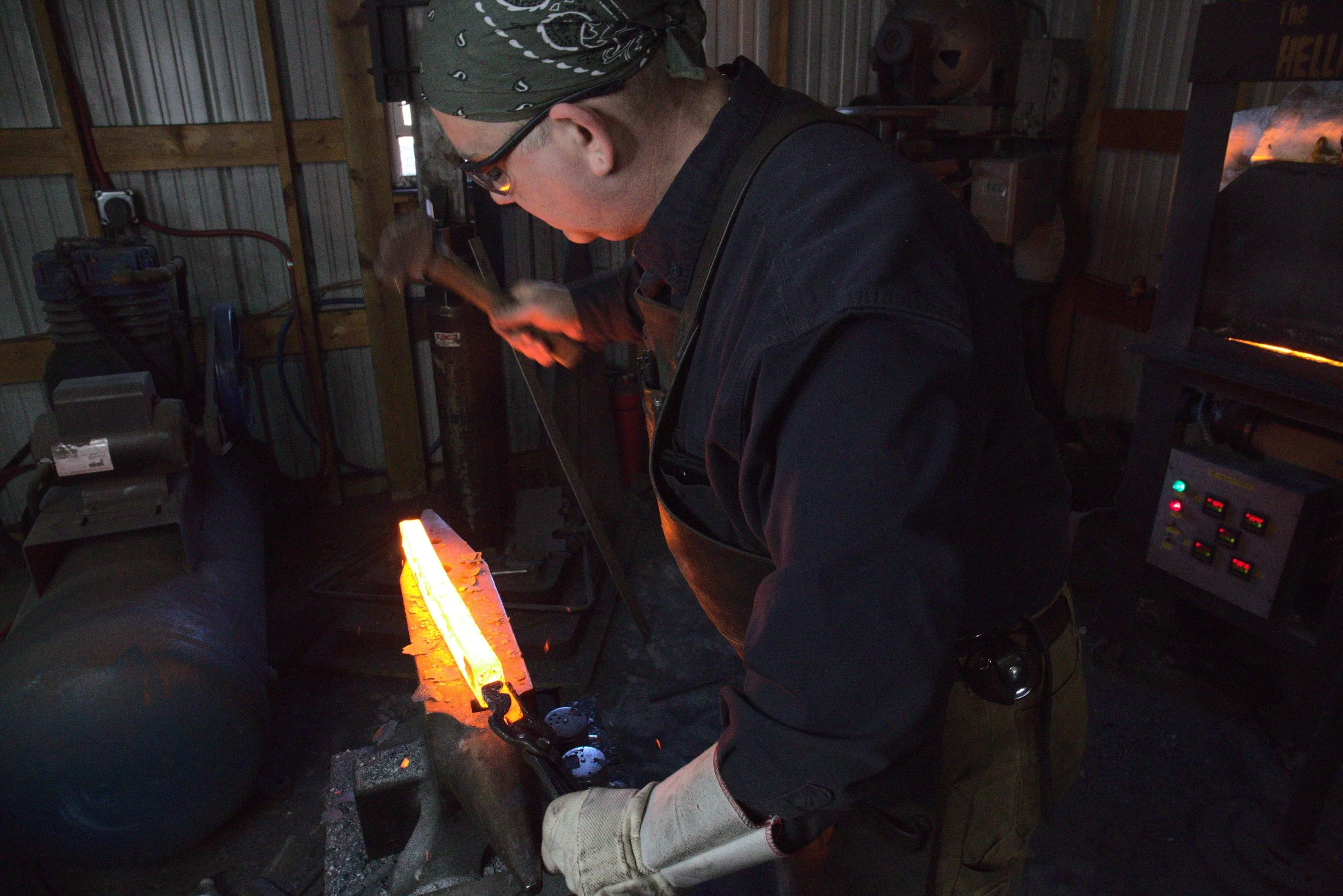



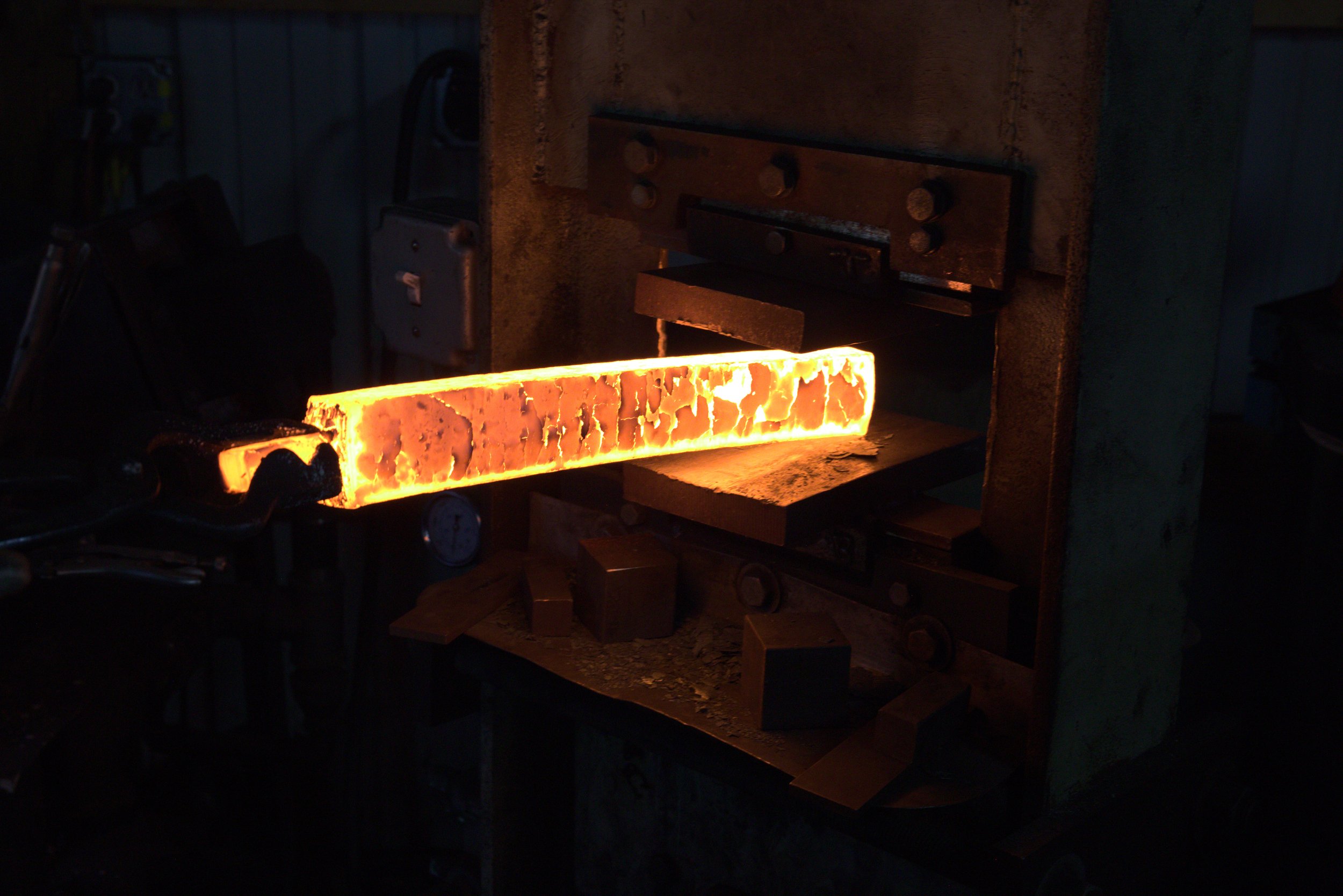
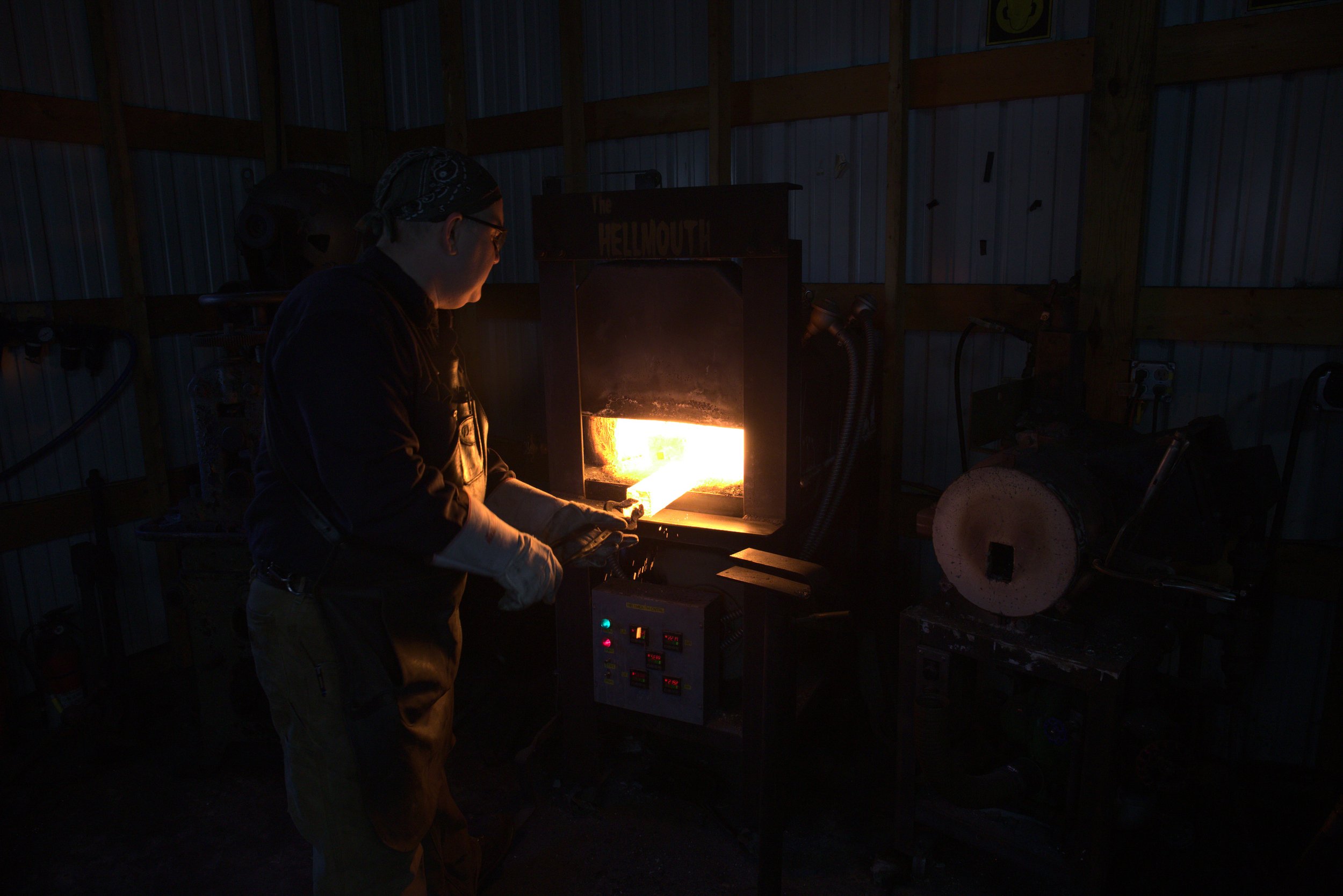




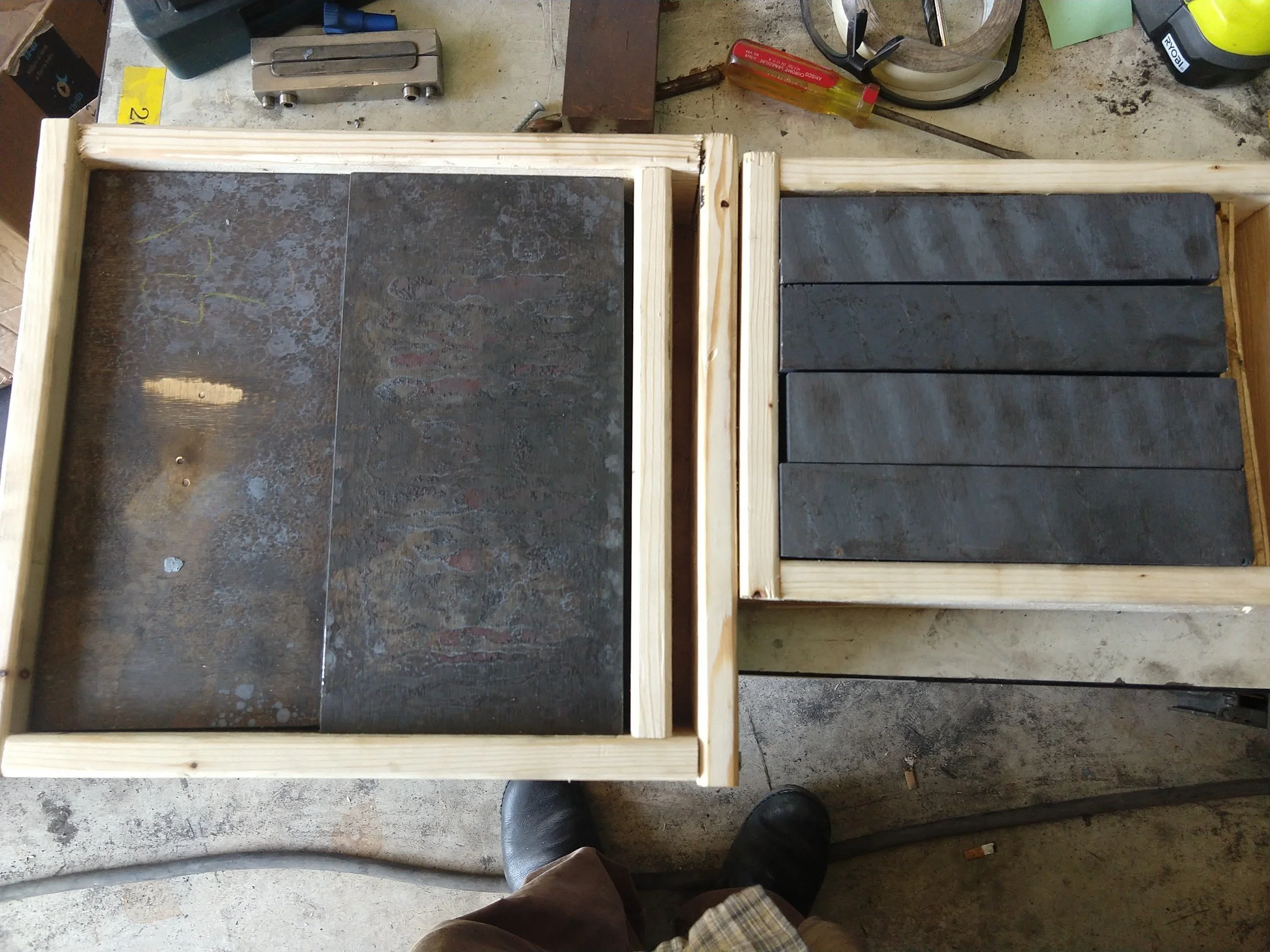